Made In India. Made To Last.
Quality & consistency that every foundation can trust.
NAGARJUNA Fe 550 TMT
The Fe 550 TMT bars manufactured at the fully automated plant of Nagarjuna Steels meet the highest international standards of weldability, ductility and bendability. The superior chemical, physical and mechanical properties of Nagarjuna TMT bars make them ideal for building shock and earthquake-prone structures. The incredible dealer network across South India and the certified standards of quality (ISO 9001-2008) make Nagarjuna TMT the obvious choice for building a stronger and long-lasting tomorrow.
Highlights
- HIGHER STRENGTH
- HIGHER UTS/YIELD RATIO
- HIGHER FATIGUE STRENGTH
- EXCELLENT DUCTILITY
- Highest Level of purity
- CONSISTENT QUALITY ACROSS THE BAR
- BEST BONDING WITH CEMENT
- TRANSPARENT PRICING
- BETTER CORROSION RESISTANCE
- EXCELLENT THERMAL STABILITY
- HIGHER WELDABILITY
- SUPERIOR DISTRIBUTOR NETWORK
Quality Objectives
- Customer Satisfaction
- Technological Innovation
- Detailed Quality Sampling
- Manufacturing Products Of The Highest Standards
- Strict Adherence To IS & ISO Standards & Procedures
Our Quality Assurance Standards
Quality has always been an essential part of Nagarjuna Steels’ DNA. Every product manufactured here goes through a strict set of procedures before being exhaustively tested to ensure that they meet international standards and customer specifications. The manufacturing process is constantly reviewed and upgraded to deliver the highest levels of efficiency and productivity.
Key Features Of Nagarjuna TMT Bars
Nagarjuna TMT’s unique chemical composition gives it higher yield strength (580 N/mm2) and tensile strength (620 N/mm2)
While TMT bars are usually highly resistant to corrosion and thermal exposure, the ones made by Nagarjuna Steels also provide high resistance to rusting and greater longevity. This makes them the obvious choice for building long-lasting and solid structures.
Nagarjuna TMT’s excellent flexibility, bendability and elongation properties make them ideal for a wide range of construction purposes. This versatility is what makes it perfect for every use.
Manufacturing Process
MELTING & REFINING
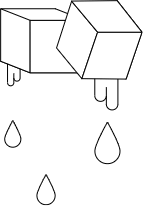
01
The raw material for our steel bars is processed in our in-house induction furnaces. Once the raw material has been melted inside the furnace, the molten metal is separated from the slag.
At this point, we purge the molten product inside a ladle furnace to achieve the desired chemical composition. During this process, we add micro-alloying materials to fix the inherent chemistry of the molten metal. At this stage, excessive non-metallic inclusions are removed from the mix. It is crucial to maintain the chemical composition in order to achieve weldability, ductility, strength and elongation during the rolling process. We keep an eye on the chemical composition with the help of our high-end spectrometer.
At this point, we purge the molten product inside a ladle furnace to achieve the desired chemical composition. During this process, we add micro-alloying materials to fix the inherent chemistry of the molten metal. At this stage, excessive non-metallic inclusions are removed from the mix. It is crucial to maintain the chemical composition in order to achieve weldability, ductility, strength and elongation during the rolling process. We keep an eye on the chemical composition with the help of our high-end spectrometer.
Molten metal from the ladle refining furnace is poured into a nearby tundish, which then pours the liquid into a mould located underneath. This process is used to cast a predetermined length of metal, transforming the molten metal mix into a solidified form. New molten metal is continuously supplied to the mould at a precise rate to keep up with the solidifying process.
Our advanced continuous casting machine helps in achieving improved yield, cost efficiency, productivity, and quality.
Our advanced continuous casting machine helps in achieving improved yield, cost efficiency, productivity, and quality.
02

CONTINUOUS CASTING

CONTINUOUS CASTING
02
Molten metal from the ladle refining furnace is poured into a nearby tundish, which then pours the liquid into a mould located underneath. This process is used to cast a predetermined length of metal, transforming the molten metal mix into a solidified form. New molten metal is continuously supplied to the mould at a precise rate to keep up with the solidifying process.
Our advanced continuous casting machine helps in achieving improved yield, cost efficiency, productivity, and quality.
Our advanced continuous casting machine helps in achieving improved yield, cost efficiency, productivity, and quality.
SECONDARY COOLING & HOT CHARGING
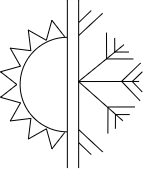
03
Once the solidifying billets exit the continuous casting machine, they enter a secondary cooling chamber. Here, the semi-finished billets are sprayed with water to achieve complete solidification. This process is important for maintaining the shape of the solidified billets, improving their quality in the long run.
Next, the solidified metal strands are reheated again in our reheating furnace. This is done to recrystallize the metal, improving quality and reducing material losses. The recrystallization process is very important because the metal strands can then be processed in the rolling mill without destroying the bonding.
Next, the solidified metal strands are reheated again in our reheating furnace. This is done to recrystallize the metal, improving quality and reducing material losses. The recrystallization process is very important because the metal strands can then be processed in the rolling mill without destroying the bonding.
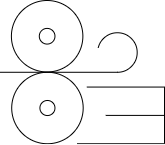
ROLLING MILL
04
The recrystallized metal billets are transported to a cutting-edge rolling mill using conveyors. Here, they are processed using the internationally accepted roll pass design, which makes for higher strength and elongation. This fully automatic process ensures a greater degree of uniformity throughout the length of each bar.
Our state-of-the-art rolling mill technology comprises a roughing mill of two 18” stands, four intermediate mills, four pre-finishing mills, and a finishing mill of six 12” stands. All the stands have individual DC motors to maintain total automation.
Our state-of-the-art rolling mill technology comprises a roughing mill of two 18” stands, four intermediate mills, four pre-finishing mills, and a finishing mill of six 12” stands. All the stands have individual DC motors to maintain total automation.
The recrystallized metal billets are transported to a cutting-edge rolling mill using conveyors. Here, they are processed using the internationally accepted roll pass design, which makes for higher strength and elongation. This fully automatic process ensures a greater degree of uniformity throughout the length of each bar.
Our state-of-the-art rolling mill technology comprises a roughing mill of two 18” stands, four intermediate mills, four pre-finishing mills, and a finishing mill of six 12” stands. All the stands have individual DC motors to maintain total automation.
Our state-of-the-art rolling mill technology comprises a roughing mill of two 18” stands, four intermediate mills, four pre-finishing mills, and a finishing mill of six 12” stands. All the stands have individual DC motors to maintain total automation.
04
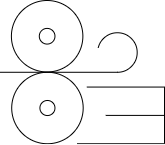
ROLLING MILL
QUENCHING & SELF- TEMPERING
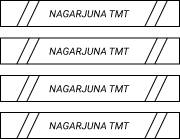
05
After the steel rebars leave the finishing mill with the desired size, they enter a water cooling chamber where they’re subjected to a quenching process. We have an Evcon Turbo machine which employs a unique method for quenching and self-tempering the ribbed steel bars. This treatment is completed in 3 successive stages:
● As soon as the steel rebars leave the final mill stand, they are rapidly cooled to ensure surface hardening.
● Once the quenching operation is completed, the surface layer of each bar undergoes a tempering process with the help of the residual heat left in its core.
● The third stage takes place when the steel bars lie on a cooling bed, where they are subjected to rapid air cooling.
● As soon as the steel rebars leave the final mill stand, they are rapidly cooled to ensure surface hardening.
● Once the quenching operation is completed, the surface layer of each bar undergoes a tempering process with the help of the residual heat left in its core.
● The third stage takes place when the steel bars lie on a cooling bed, where they are subjected to rapid air cooling.
Due to this extensive process, each of our steel bars have greater strength, ductility, bendability and weldability.
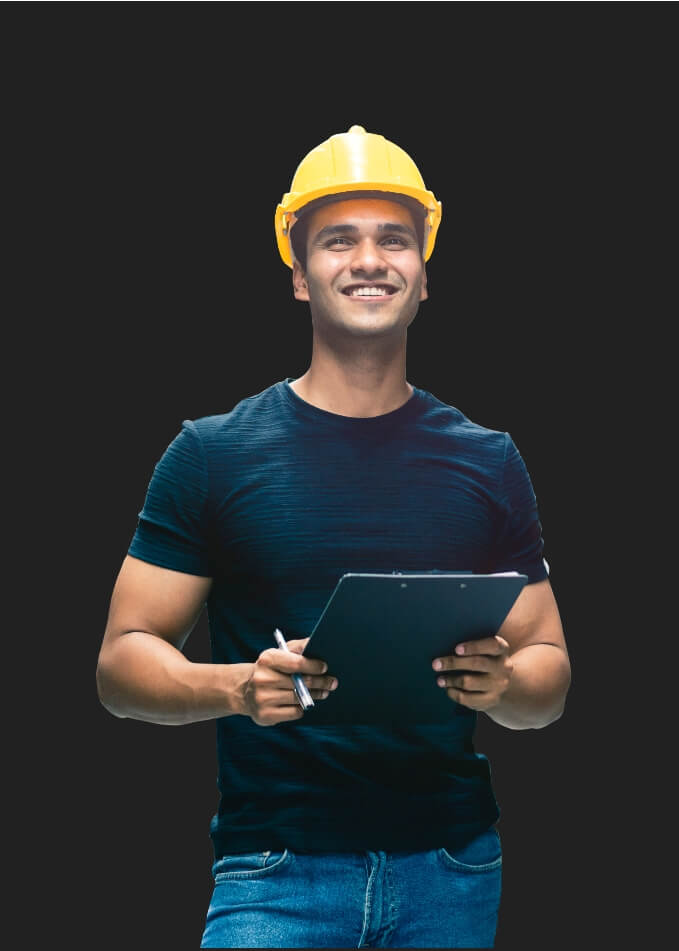